Detail Engineering and Implementation of Polymer/Resin Batch or Semi Batch Plants:
Crown: Polyvinyl Chloride Plant (PVA) with commissioning
National Adhesives/Unilever: Resins Alkyd Resin Plant with commissioning
International Paints Company (IPC) a subsidiary of Courtaulds: Polyester and various Speciality Resins Plant Complex
Bonar Polymers: Debottlenecking of an Acrylic Polymer Plant
Polymer Latex (subsidiary of BAYER): NBR Polymer Plant complete with refrigeration facilities (2 x 450kW units)
Polymer/Resin Plant
Detail Engineering of Continuous Polymer Plants:
Design and development of control and sequence interlocks and cause & effect charts for a 100,000 tonnes per annum of MMA (methylmethacrylate) monomer plant for copolymers, resins, paints, dispersions and coatings and other applications. The process involves a continuous direct oxidation and esterification production process for the plant based in Leuna, Germany using licensed technology from Asahi.
Detail engineering and implementation of major relief systems for an LDPE Plant (Low Density Polyethylene) for PTTP in Thailand. The process essentially comprises polymerisation of ethylene gas at high pressures using primary compression at circa 300 bar g and secondary/hyper compression at circa 2500 bar g to 3100 bar g. Polymerisation takes place in a tubular (plug type) continuous reactor. Relief systems were designed for the low design pressure equipments ie below 300 bar g and 3100 bar g (heat exchangers and various vessels) and piping configurations downstream of both compressors. The back pressures were determined for relief scenarios on the low design pressure equipments and the flare header pressures were taken into consideration. The design was implemented for construction.
Polymer Plant Design Studies and Basic Engineering:
Basic Engineering on a Formaldehyde plant and urea formaldehyde resin plant for Caperboard complete with conveying facilities of solids
Site based Design work for GE Plastics covering handling of ABS pellets and their conveying to other parts of the plant. Design of Receipt of pellets, sampling, pneumatic transfer, silos storage, weighing and automatic product bagging inside booths and the design of venting facilities.
Polymer Batch Plants essentially comprising of the following:
Receipt of bulk chemicals (monomers, additives, etc) from tankers and and their storage in tank farm
Raw materials feeds and additives into reactors with solids charging (eg phthalic anhydride) using screw conveyors
Polymerisation of monomer in reactors
Reactor Product Discharge
Heating and Cooling and Condensers
Filtration and Blending
Monomer and Solvents Recovery by Distillation
Storage of Intermediates and Products – for dispatch via tankers
Reliefs
Safety with respect to flammability, explosive mixtures including dust and hazardous materials handling.
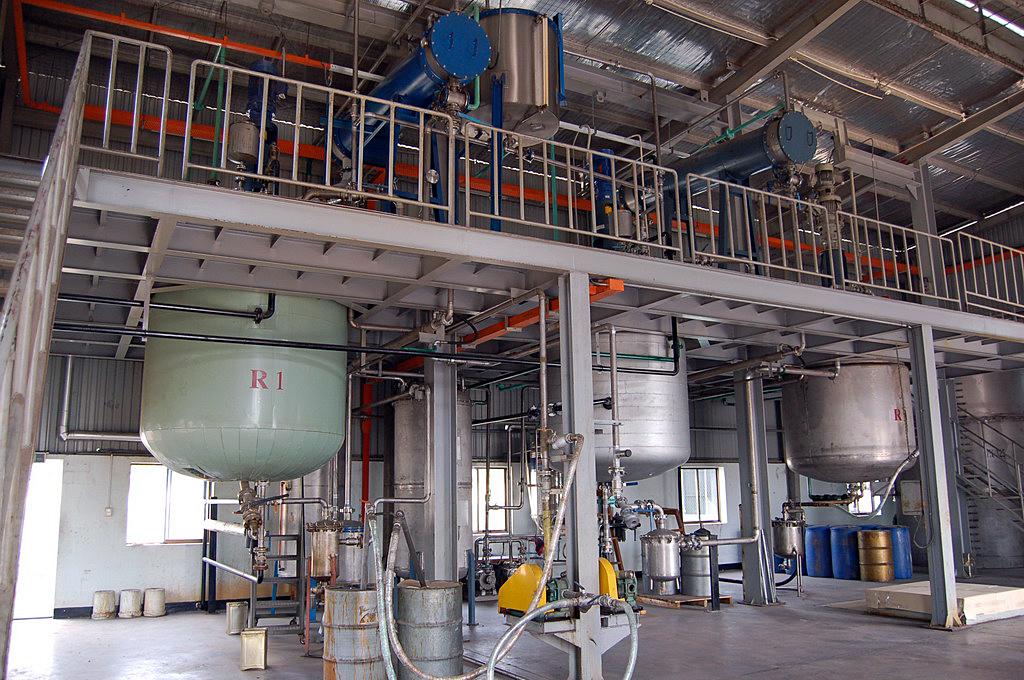
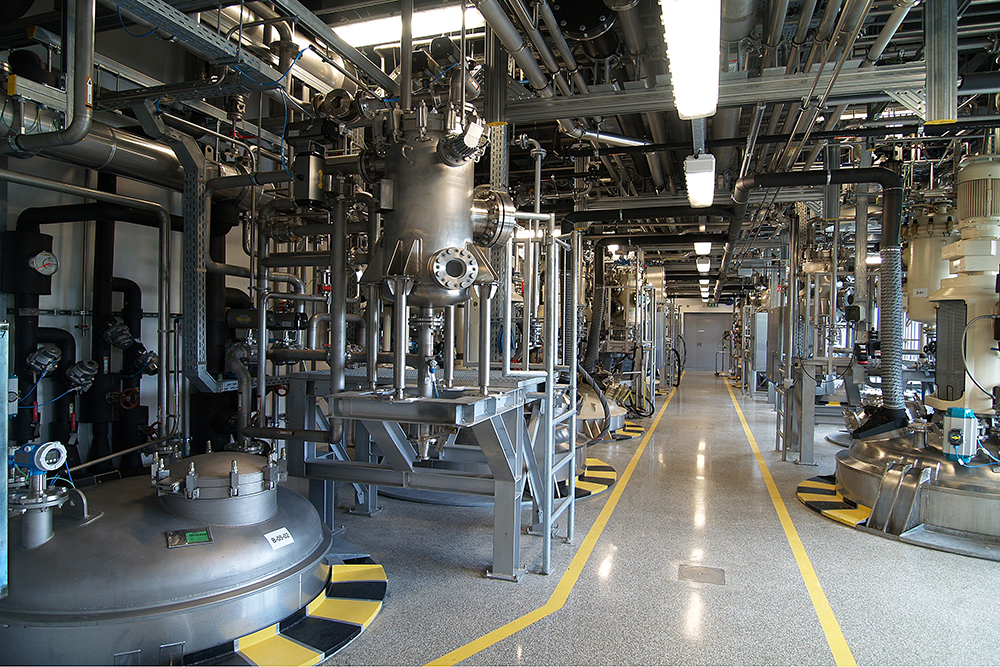
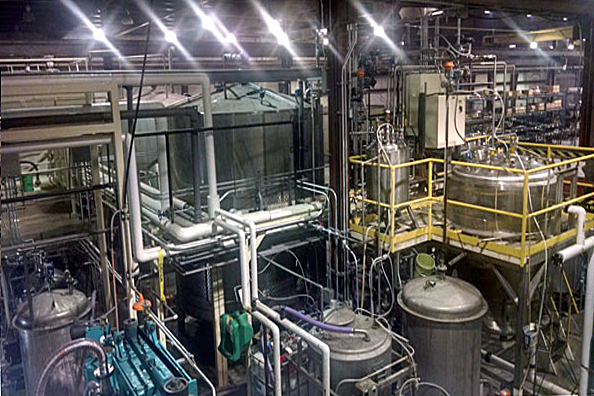
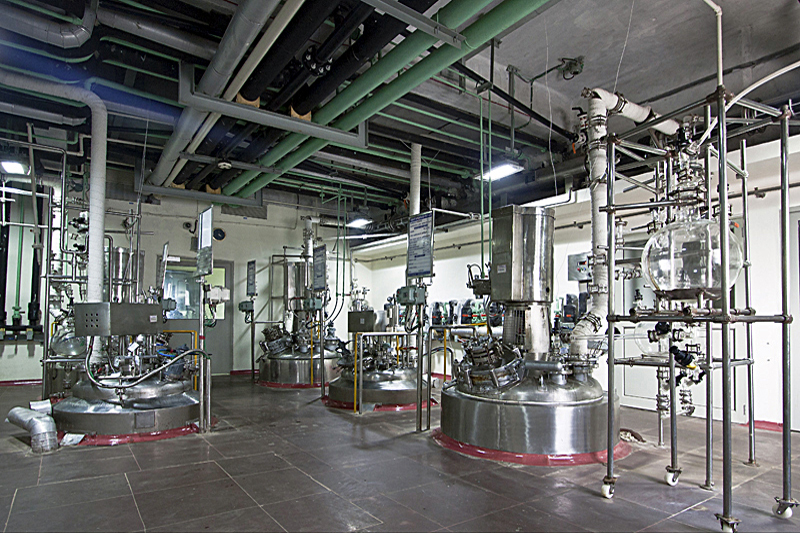
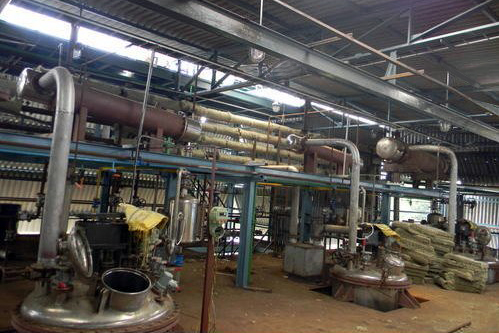