CHEMICALS:
ICI Paraquat Plant (Continuous Process). Site based Detailed engineering and implementation of the modifications for general improvements and to minimise emissions. Comprising new control valves and control loops, pumps, pipe fittings, sampling facilities, modes of storage facilities, vents, reliefs and modifications to centrifuging facilities
EVC (ex ICI): Detail engineering on an ethylene dichloride (EDC)/vinyl chloride plant stream and the rejuvenation/debottlenecking of an existing plant for EVC (European Vinyl Corporation). Engineering work covered the following: Ethylene centrifugal compressor, High pressure nitrogen PD compressor, Gas drying, Filtration, Reactors (Fixed Bed Reactor and Fluidised Bed Reactor – production of EDC by reacting HCl with ethylene), Stripper, Heat Exchangers, Pumps, Pressure Vessels and Reliefs
New liquid argon facilities comprising tanker receipt, storage and distribution facilities of the gas for the EP1/EPS1 Project for BNFL at Sellafield
EP2: Detail design for the receipt of HCl and Cuastic from road and rail tankers, Storage and distribution facilities to the plant users at Sellafield
Specialist design for the production of a Standard Design (ie “Signature Design”) for Montgomery Watson Harza (MWH) for road tanker receipt, storage, handling and discharging of bulk chemicals, ie Caustic and Sulphuric Acid.
Cabot Carbon: Basic engineering for a Carbon Blacks Plant complete with feedstock oil tanker receipt, bulk raw materials storage, handling and distribution of oil, tail gas flare, reactor/burner, filtration facilities of smoke header gases, spent hot fuel gases for steam (boiler) generation. Product storage facilities in silos, solids conveying and bagging/packaging facilities.
Bulk methanol receipt, storage and distribution. Complete with design of water deluge and fire prevention facilities
Butanol and Methylene Chloride distillation for Roche, Dalry, UK.
Process plant modifications for Yamanouchi, Ireland. Provision of the design for HCl gas safe receipt, bulk handling of containers, storage and distribution of the gas on site. Review of existing gas facilities (SO2 containers and Nitrogen bottles) with improvements.
B&N Chemicals: Formaldehyde Plant expansion design study and expansion of tank farm facilities
Neoprene production at Maydown Works, Londonderry, for DuPont
New Tar Distillation Plant Complex (150 tons per day) for Dankuni, India. Design of tar dehydration column, primary tar distillation , fractionating column for tar product streams, crude tar acids recovery (Phenols, Cresols and Xylenols) by extraction, caustic washing, CO2 contacting or “Springing” and vacuum distillation in stills to attain high purity tar acid products. Recovery and blending of various tar oils (Light, Naphtha, Creosote and pitch). Pitch blending. Storage of raw materials, intermediates and products. New plant for Effluent treament comprising aerators, clarifiers/sludge sedimentation and disposal.
Tar Distillation Plant for Coal Tar Refinery (CTR) in Tehran for the Esfahan Steel Project. Basic engineering with initial pilot plant work done at BCRA, Avenue, Chesterfield. Comprising pilot plant primary distallation of coal tar and evaluation of products attainable economically (Tar Oils, Naphthalene, Tar Acids, Pitch of various grades ie Binder, Impregnation, Softening) . Overview of the Basic Design.
New Anthracene Paste Plant for El Nasr, Egypt. Detail Engineering to implementation comprising anthracene oil treatment, cooling, crystallising, centrifuging and bagging/palletising of anthracene paste.
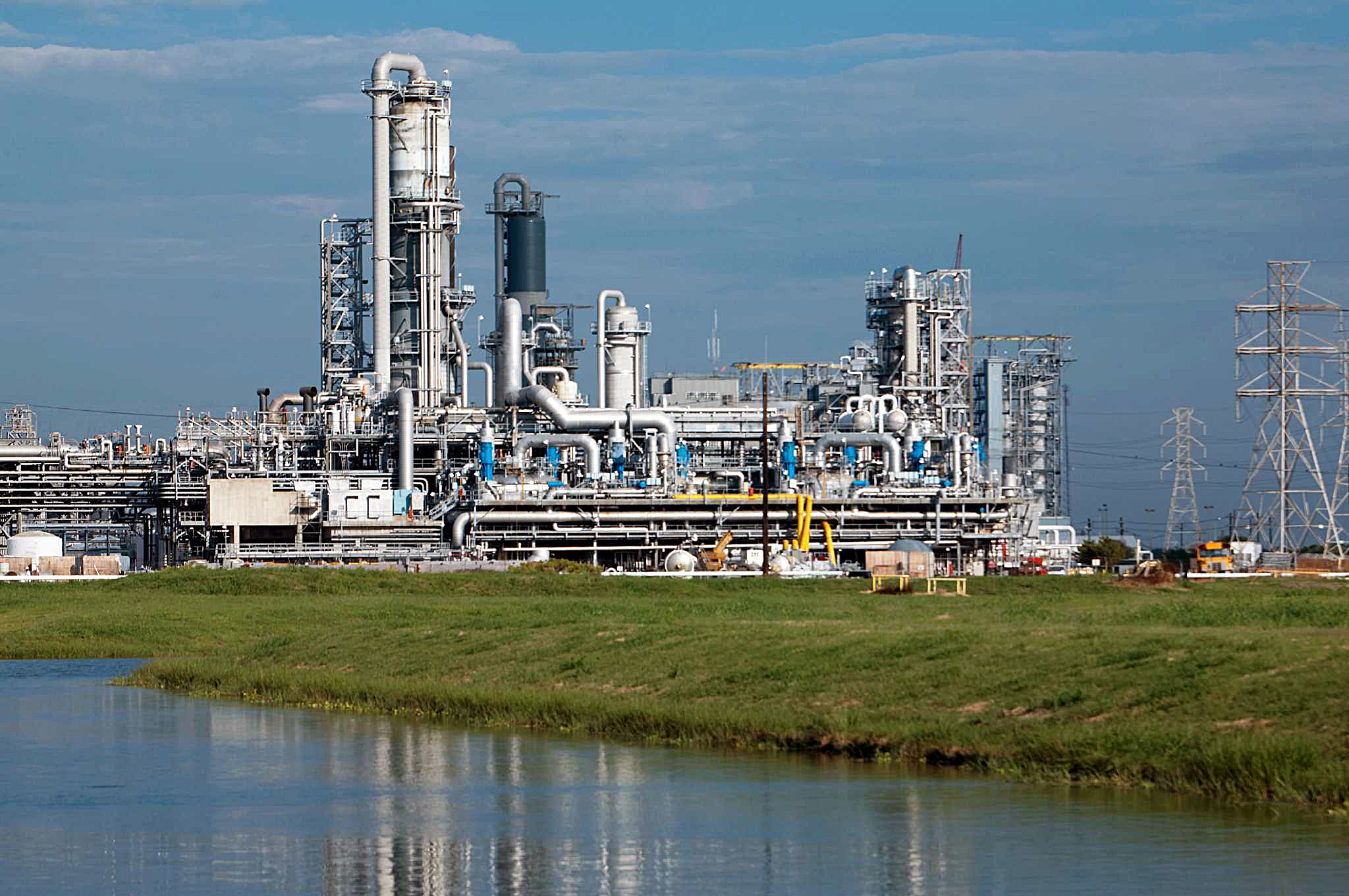
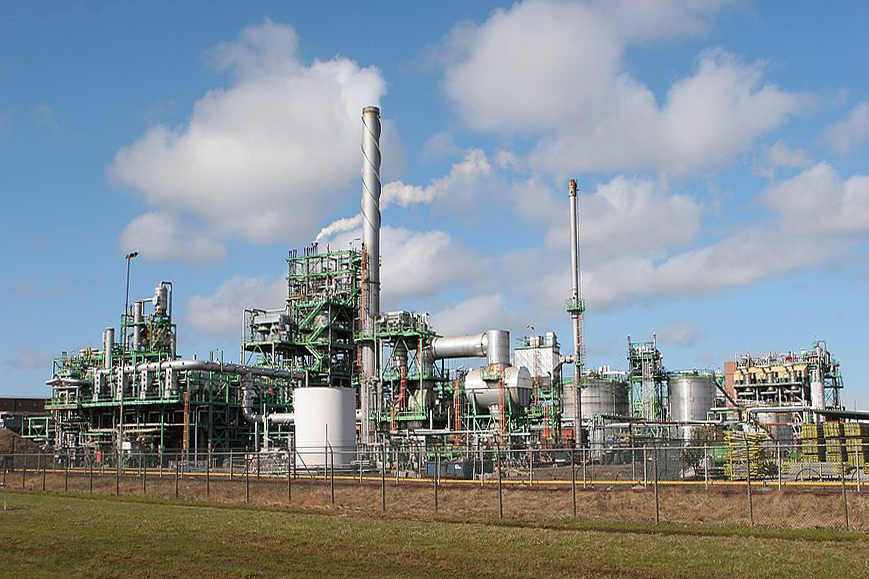
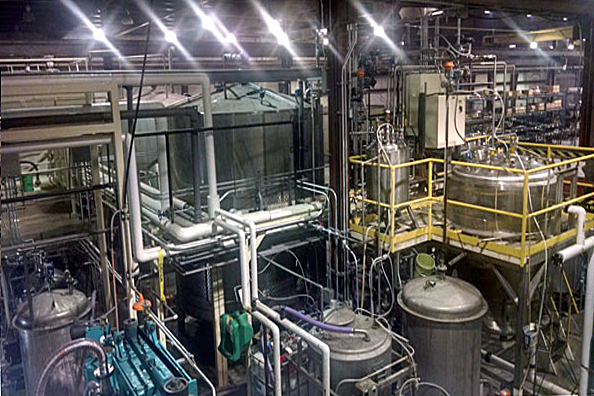
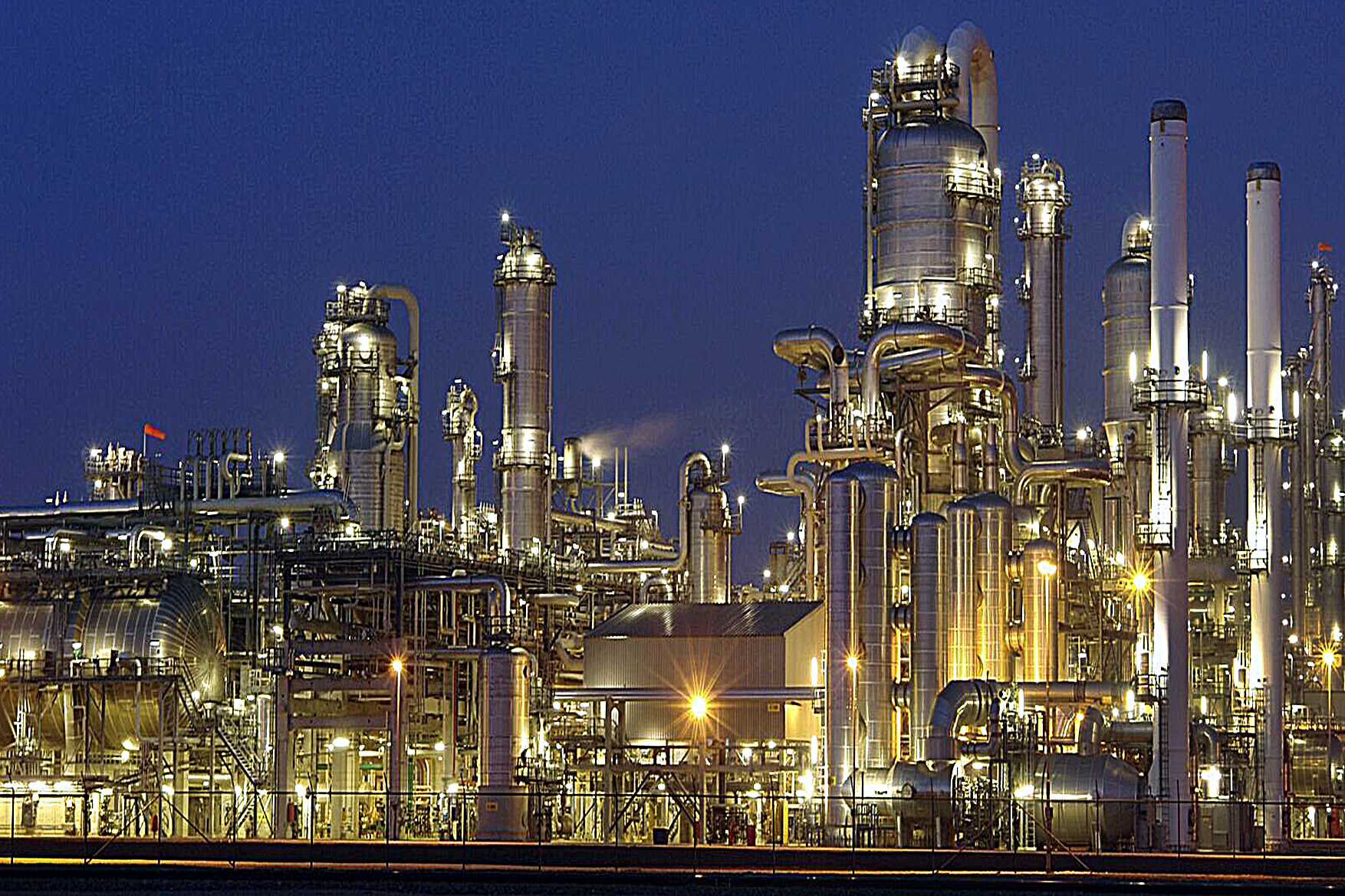
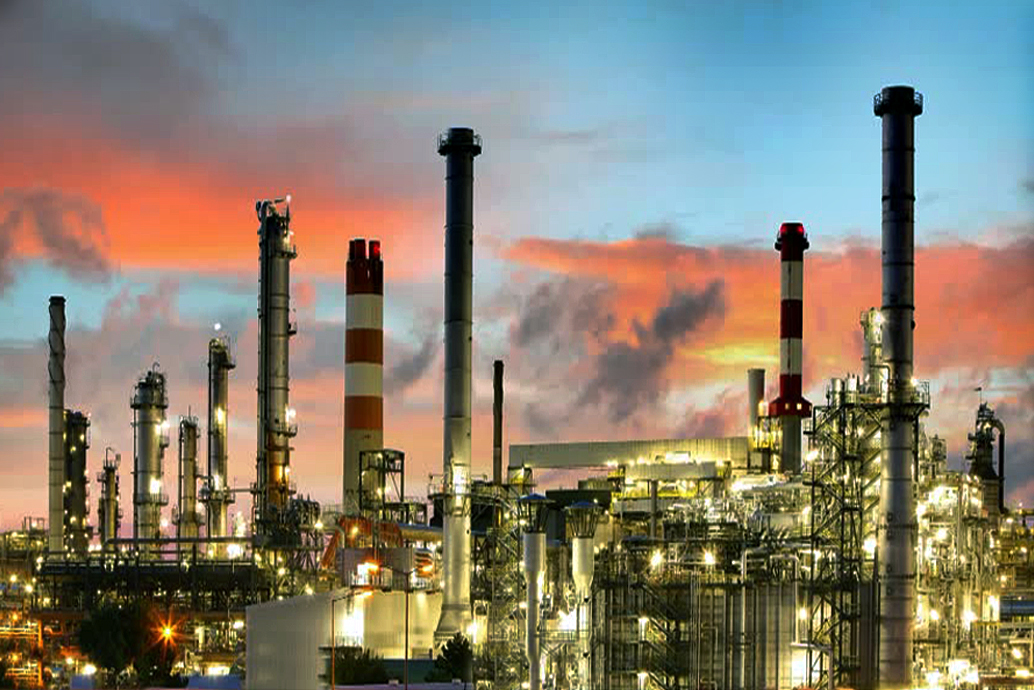
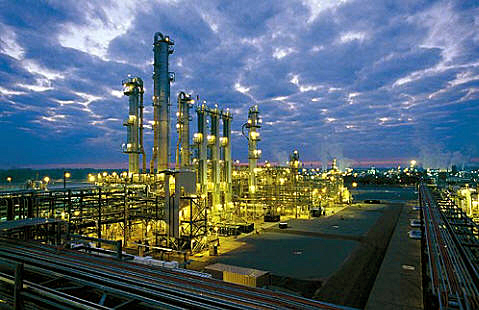
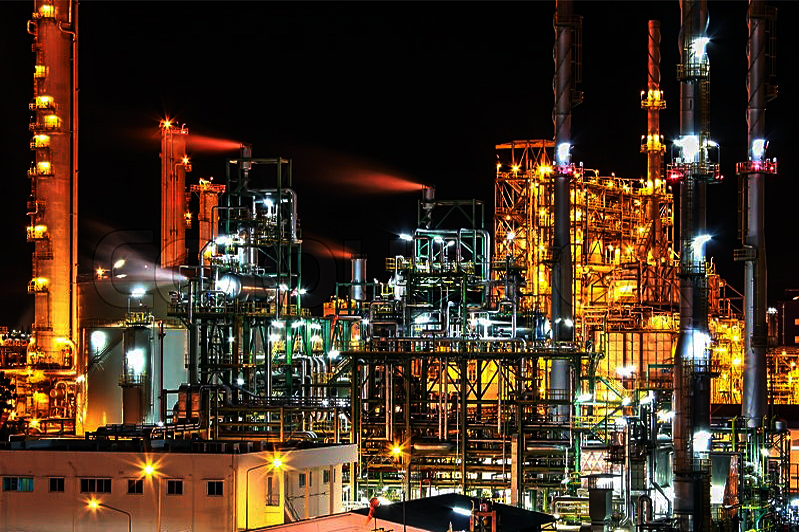